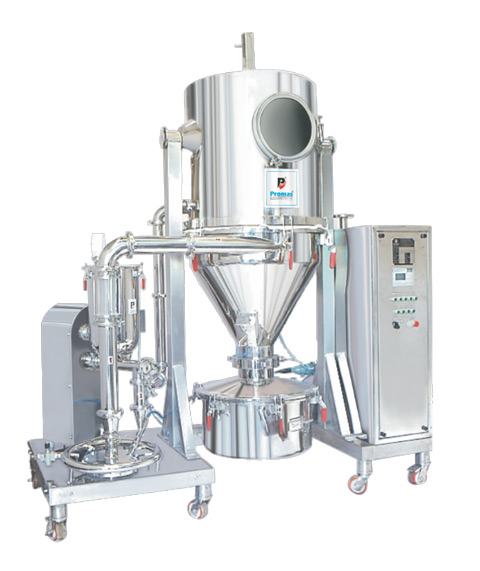
Fully Automated And Manual Jet Mill Micronizer
Jet Mills are widely used in the manufacture of drugs and pharmaceuticals, organic and inorganic pigments, optical brighteners, fluorescent pigments, food colour synthetic dyes, metal (except malleable metals) carbides & borides, herbicides and pesticides, ceramic glasses, alumina, feldspar, frit, kaolin, mullite, electronic grade materials such as materials required for semiconductors, phosphors, photo electronic, high temperature critical materials and rocket solid fuels etc. We are manufacturer, supplier and exporter multiple variety manual and fully automated jet mill micronizer, micro pulverizer and spiral fluidize air with industrial requirement.