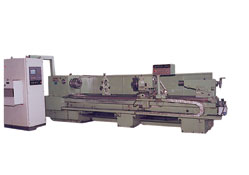
Flat Bed Lathes Cnc
Designed to provide flexible, accurate, and cost effective machining (such as chucking jobs, shaft turning, OD/ID, profile turning and thread cutting).
Salient Features :
» Infinitely variable spindle speeds, selectable in two automatic ranges.
» Optional 12-station tool turret in lieu of standard 8-station.
» Rigid tailstock with hardened and ground guideways.
» High precision antifriction bearings for the hardened and ground main spindle.
» Hardened and ground bed guideway.
» Both longitudinal and transverse axis (Z & X) are by ballscrews and AC servomotors with encoder feed back.
» Carriage and cross slide guideways are fixed with antifriction turcite liners for stick slip free movement.
» 8-station bidirectional tool turret . 12-station turret optional.
» Rigid tailstock with hardened and ground sleeve. Can also by supplied with optional rotating centre.