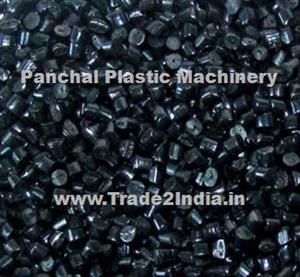
Black Masterbatch
Our technological adeptness has made us the pioneers of manufacturing and supplying high quality Black Masterbatch. These products are widely recommended for its superior resistance to high temperature which makes it the most suitable Masterbatch for processing pipes, cables, and mulch films. Processed from ultra-fine carbon and PE additives the offered wide range of Black Masterbatch is developed under strict quality regulations to meet the standards of excellent dispersion qualities. Further, our prestigious clients can order varied grades of Black Masterbatch from us at the best price in the industry.
Advantages of Black Masterbatch:
Excellent weatherabilty
High Jetness
Uniform Particle Size
Excellent dispersion
Smooth surface